- Published on
From BIM to Digital Twins: Optimizing Operations & Facility Management
- Authors
- Name
- Jane Sison
- about
In today’s built environment, the transition from Building Information Modeling (BIM) to Digital Twins is reshaping how facilities are managed and operated. This evolution unlocks new opportunities to enhance efficiency, reduce costs, and improve asset performance throughout the entire lifecycle. In this article, we explore how a BIM model can be developed into a Digital Twin for Operations and Facility Management (FM), along with the real-world benefits of doing so.
What is a BIM Model?
Building Information Modeling (BIM) is a digital representation of a facility’s physical and functional characteristics. It serves as a shared information resource, supporting collaboration across the design, construction, operations, and maintenance phases. BIM goes beyond 3D modeling, encompassing additional dimensions such as time (4D), cost (5D), and asset management (6D), including maintenance and operational data.
BIM Digital Twins for Rich Data Visualization
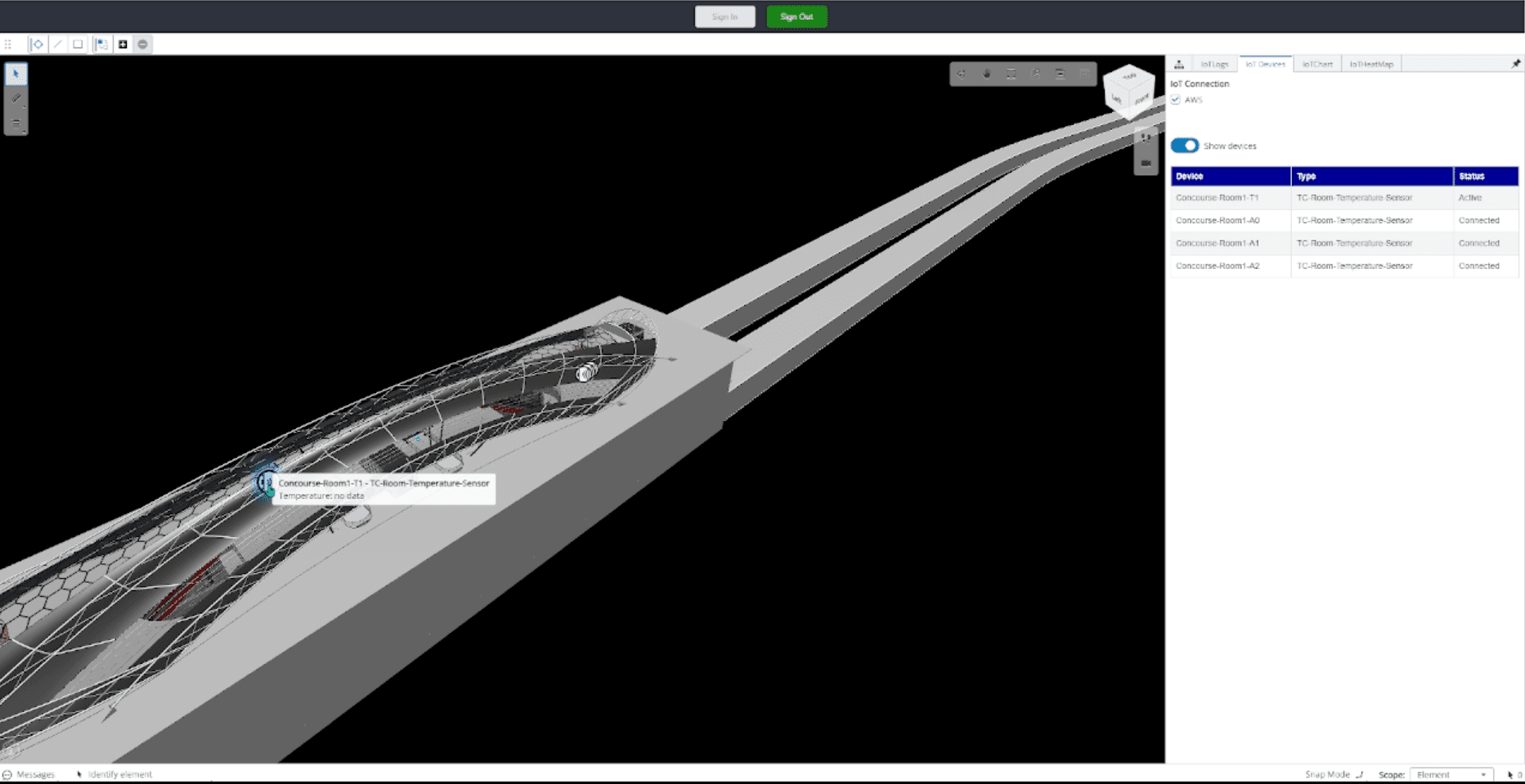
A digital twin is a dynamic virtual model that mirrors a physical asset in real time. Powered by live data from IoT sensors, digital twins enable continuous monitoring, simulation, and optimization. They can represent anything from individual components to entire buildings and urban environments, offering powerful insights for performance management and predictive maintenance.
Steps to Creating a Digital Twin from BIM
1. Identify Critical Use Cases
Define the key objectives for your digital twin—such as predictive maintenance, energy efficiency, or safety monitoring. Clear use cases help guide the design, sensor selection, and data integration strategy needed to deliver measurable value.
2. Create the Visual Context
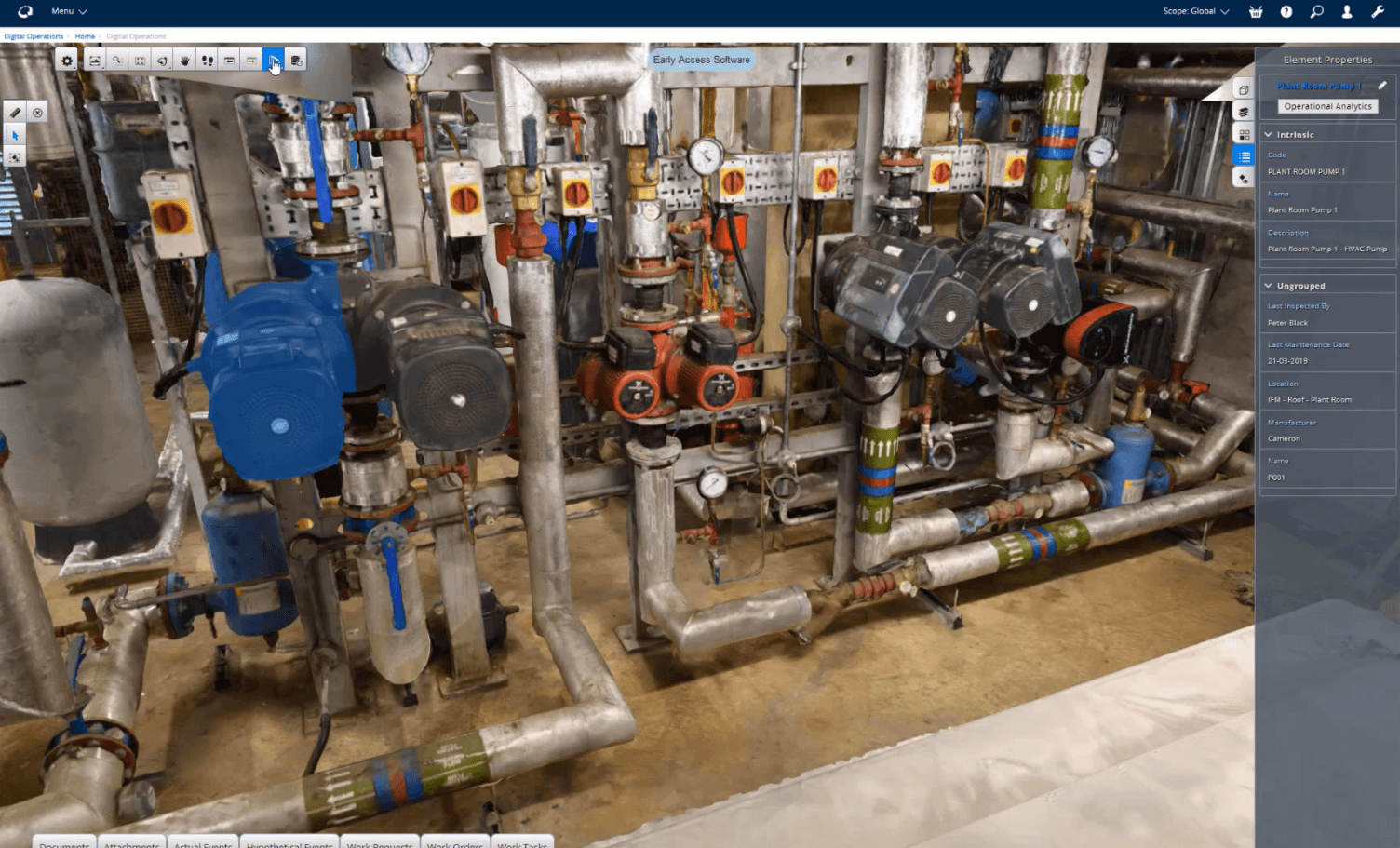
Develop a comprehensive BIM model that accurately reflects the current state of the asset. For newer projects, 3D BIM models make it easier to establish the visual context of the digital twin. Asset data and equipment tags can be incorporated into the BIM model to enhance its utility.
If 3D models are unavailable, 2D drawings can also be used to build a 3D model. The goal is to create a digital twin that closely matches the physical asset.
3. Integrate Operational Data
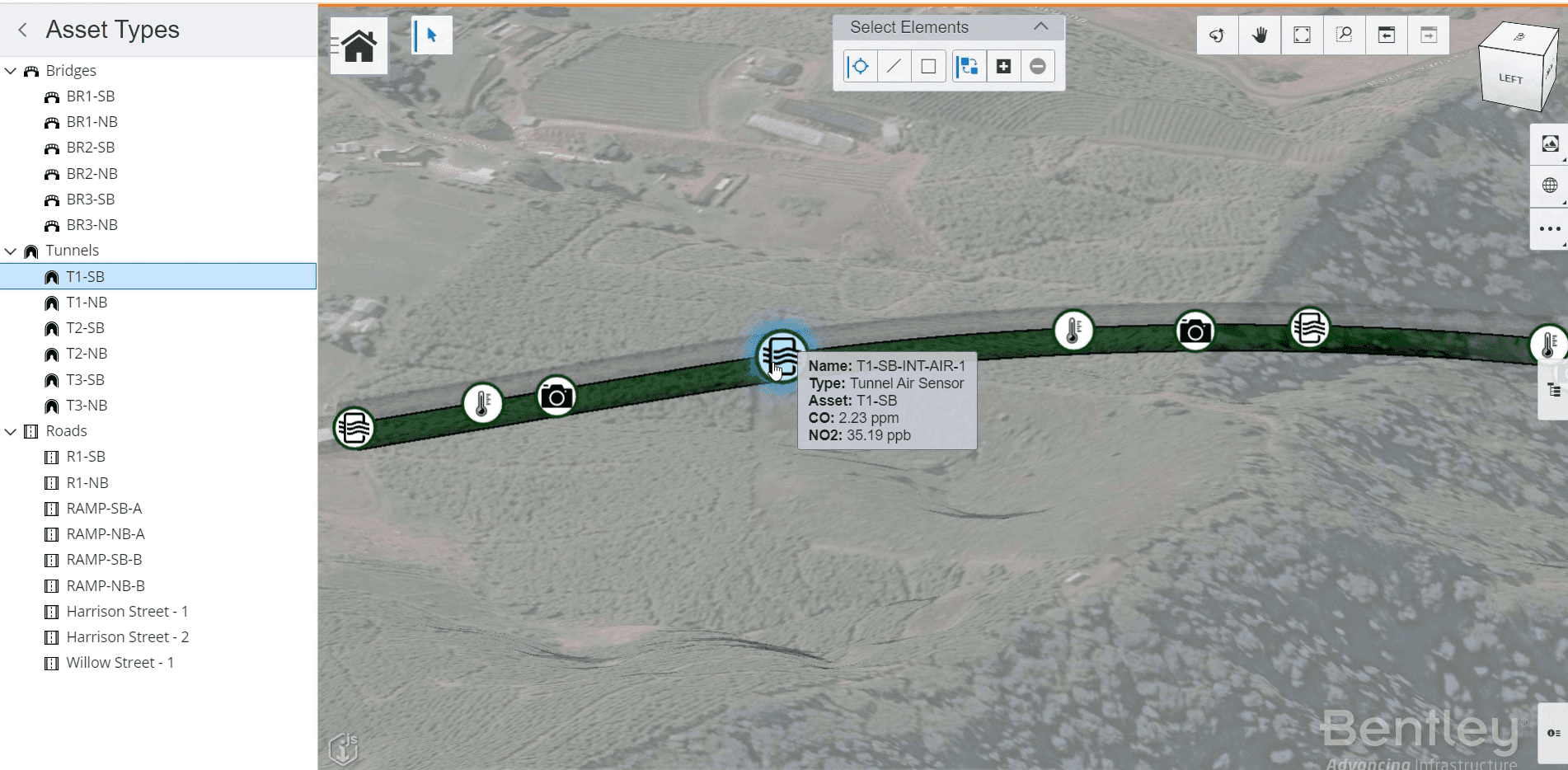
Install IoT sensors to collect key operational metrics like temperature, humidity, vibration, and energy usage. Most buildings already have Building Management Systems (BMS), which can be integrated into the digital twin. By accessing BMS via Open API interfaces, real-time data can be captured and incorporated into the digital environment.
4. Perform Simulation and Analysis
With both geometric and live operational data in place, you can run simulations, detect anomalies, and forecast performance trends. These predictive insights support proactive facility management, optimize resource usage, and extend asset lifespans.
Benefits of Transitioning to a BIM Digital Twin
📊 Improved Asset Performance
Digital twins provide real-time analytics that enhance asset utilization and operational efficiency. In sectors like healthcare, they enable continuous monitoring of critical systems, improving patient care and ensuring regulatory compliance. For facility managers, the digital twin serves as a navigable, data-rich interface—allowing operators to quickly identify and locate problematic areas within the facility. Integrated mobile applications enable teams to update issue statuses, track resolution progress, and ensure timely follow-up, all while working on-site or remotely.
🔧 Predictive Maintenance
By continuously monitoring asset conditions, digital twins enable early fault detection—minimizing unplanned downtime and reducing maintenance costs. When integrated with 6D BIM, they centralize critical information such as maintenance histories, equipment specifications, and sensor feedback. This unified data environment supports more accurate diagnostics, proactive planning, and streamlined maintenance workflows.
🌐 Remote Monitoring
Digital twins enable secure, real-time access to operational data from anywhere, improving responsiveness and reducing the need for on-site inspections. Maintenance teams can remotely diagnose and resolve issues, enhancing safety and efficiency. In addition, the digital twin environment supports immersive training simulations, helping technicians build familiarity with complex systems before setting foot on-site.
Begin Your Journey from BIM to Digital Twins
Successfully transitioning from BIM to a Digital Twin requires thoughtful planning—from developing accurate models and selecting the right sensors to deploying reliable cloud infrastructure. When implemented well, this transformation supports smarter decision-making, improves asset performance, and yields long-term cost savings.
As the AEC industry continues to embrace smarter facility management practices, integrating BIM and Digital Twins is emerging as a key strategy for achieving safer, more sustainable, and more efficient building operations.